Break the normal procedure ,Cutting carbon steel in this way saves 1.1 million RMB a year.
In the traditional laser cutting of carbon steel, oxygen is generally selected. With the continuous progress and breakthrough of high-power laser cutting technology, Maxphotonics technology application department breaks the routine and applies nitrogen, oxygen and air to different materials according to different cutting requirements, which can not only improve the cutting efficiency, but also reduce the terminal processing cost.
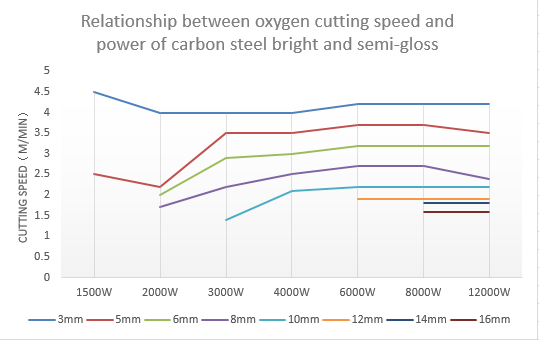
Reasons for choosing different gases:
1. For any thickness of carbon steel, there is a limit speed when using oxygen cutting, even if the laser power is increased, the cutting speed remains unchanged;
2. High power laser uses oxygen to cut medium and thin plate carbon steel, so as to prevent over burning caused by high power, so laser power must be reduced;
3. The 10,000-watt laser uses oxygen to cut medium-thick carbon steel without speed advantage, but increases processing costs.
Gas selection of traditional laser cutting | |
Material | Auxiliary gas |
Carbon steel | Oxygen |
Stainless steel | Nitrogen |
VS
Maxphotonics 10000-watts Laser Cutting Gas Selection | |
Material | Auxiliary gas |
Carbon steel | Oxygen |
Nitrogen | |
Air | |
Stainless steel | Nitrogen |
Air |
Different gas cutting carbon steel processing efficiency
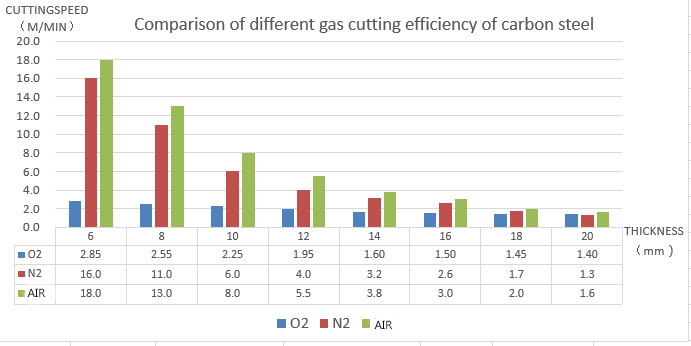
From the above test data:
1. Carbon steel 6-20mm thick plate, 12KW cutting machine using air than oxygen cutting efficiency increased by 14% -532%;
2. Carbon steel 6-20mm thick plate, 12KW cutting machine using air than nitrogen cutting efficiency increased by 11%-27%.
Different gas cutting carbon steel processing costs
From the above test data:
1. Carbon steel thickness 6-16mm, 12KW cutting machine processing cost (air <nitrogen < oxygen);
2. Carbon steel thickness 18-20mm, 12KW cutting machine processing cost (air < oxygen < nitrogen).
Annual processing cost of carbon steel for different gas cutting
From the above test data:
1.12KW cutting machine uses air-cut carbon steel, which can save processing cost of 1.1 million yuan per year;
2. Carbon steel thickness is 6-16mm, the thinner the plate, the more cost-effective to process.
Different gas cutting carbon steel sample effect
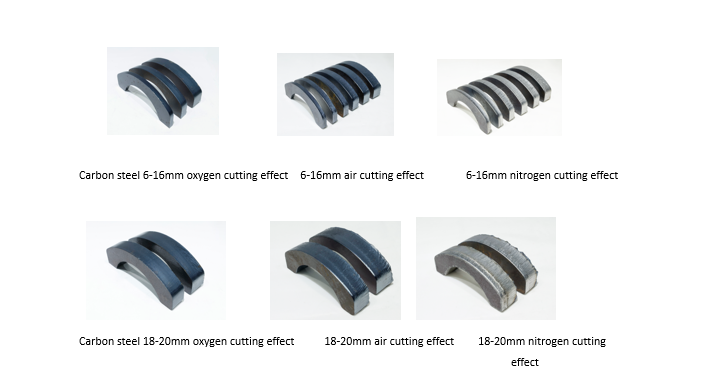
Carbon steel 18-20mm oxygen cutting effect 18-20mm air cutting effect 18-20mm nitrogen cutting effect
Summary of cutting effects of different thicknesses of carbon steel | |||
Thickness | Auxiliary gas | cutting effect | |
Section color | Drossing situation | ||
1-12mm | Oxygen | Black glossy | No dross |
Air | Black sand surface | No dross | |
Nitrogen | White sand surface | No dross | |
14-16mm | Oxygen | Black glossy | No dross |
Air | Black sand surface | Slight slag hanging | |
Nitrogen | White sand surface | Slight slag hanging | |
18-20mm | Oxygen | Black glossy | No dross |
Air | Black sand surface | Serious dross | |
Nitrogen | White sand surface | Serious dross |
It can be seen from the above test data:
Maxphotonics 10,000 watt laser cutting best gas selection | |||
Thickness | Auxiliary gas | Advantage | Disadvantage |
1-12mm | Air | Low processing cost efficient No dross | none |
14-16mm | Air | Low processing cost efficient | Slight slag hanging |
Oxygen | Good effect No dross | Low efficiency | |
18-45mm | Oxygen | Good effect No dross | Low efficiency |
1. 10,000 watt laser cutting machine processing carbon steel 6-16mm, using air to cut than oxygen, the maximum processing cost can be saved 1.1 million yuan a year;
2. The 10,000-watt laser cutting machine processes carbon steel 6-16mm, and the air-cutting efficiency is increased by 532%-100%;
3. The 10,000-watt laser cutting machine processes carbon steel 6-16mm, and the cost of using air is 85%-51% lower than that of oxygen cutting;
4. 10,000-watt laser cutting machine processing carbon steel 22-45mm, using nitrogen and air cutting, serious slag, and processing costs have no advantage, it is recommended to use oxygen cutting to ensure the cutting effect.
Laser used for testing: 12000W multimode continuous fiber laser
High Electro-optical conversion efficiency;
Meet the requirements of thick plate laser cutting, laser welding and laser cladding,surface heat treatment;
Widely used in hardware, medical, automotive, marine, aerospace, engineering machinery and other fields.
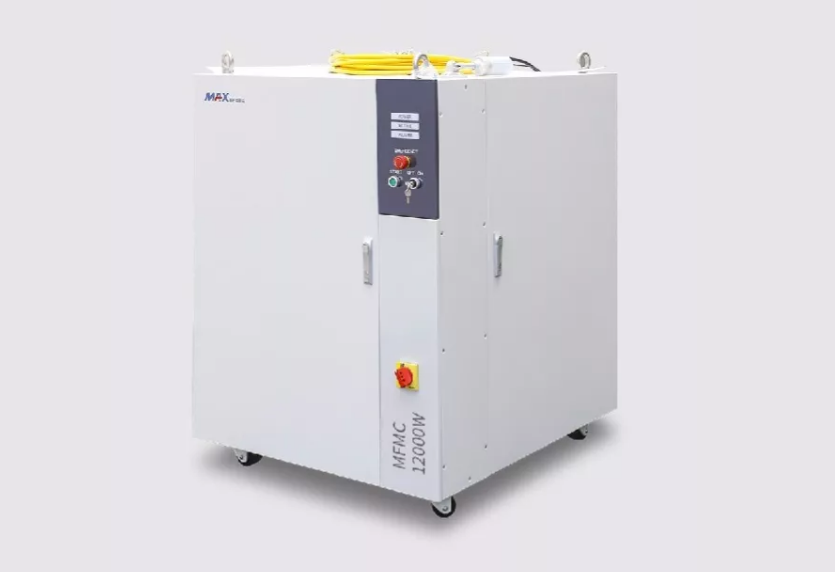